14 Management Principles From The World's Greatest Manufacturer

Toyota is the world's largest automaker, and it has been consistently ranked as one of the most admired companies in the world. Toyota's success is due in large part to its unique management philosophy, which is based on 14 principles.
4.8 out of 5
Language | : | English |
File size | : | 15513 KB |
Text-to-Speech | : | Enabled |
Screen Reader | : | Supported |
Enhanced typesetting | : | Enabled |
X-Ray | : | Enabled |
Word Wise | : | Enabled |
Print length | : | 449 pages |
These principles are not just theoretical concepts; they are practical tools that can be applied to any business to improve efficiency, quality, and profitability.
In this article, we will discuss each of the 14 Toyota management principles in detail and provide examples of how they can be applied to your business.
1. Challenge the status quo
Toyota is always looking for ways to improve, and it encourages its employees to challenge the status quo. This means being willing to question existing procedures and to come up with new and better ways of ng things.
For example, Toyota engineers challenged the traditional way of building cars by developing a new production system that is more efficient and less wasteful. This system, known as the Toyota Production System, has been adopted by many other manufacturers around the world.
2. Kaizen: Continuous improvement
Kaizen is a Japanese philosophy that means "continuous improvement." Toyota believes that there is always room for improvement, no matter how good things are.
Toyota employees are encouraged to make small improvements to their work processes on a daily basis. These small improvements can add up to significant gains over time.
For example, a Toyota assembly line worker might suggest a change to the way a particular part is installed. This change might save a few seconds per car, but when multiplied by the number of cars produced each year, it can result in significant savings.
3. Genchi genbutsu: Go and see for yourself
Genchi genbutsu is a Japanese phrase that means "go and see for yourself." Toyota believes that it is important to go to the source of a problem to understand it fully.
For example, if a Toyota manager is having problems with a particular supplier, he or she will go to the supplier's factory to see the problem firsthand. This allows the manager to better understand the problem and to come up with a solution that will work.
4. Respect for people
Toyota believes that its employees are its most valuable asset. The company invests heavily in training and development, and it provides its employees with a safe and supportive work environment.
Toyota also encourages its employees to participate in decision-making. This helps to create a sense of ownership and pride among employees, which leads to better results.
5. Teamwork
Toyota believes that teamwork is essential for success. The company encourages its employees to work together to achieve common goals.
Toyota also uses a system of cross-functional teams to break down barriers between different departments. This allows employees to share knowledge and expertise, which leads to better decision-making.
6. Jidoka: Automation with a human touch
Jidoka is a Japanese word that means "automation with a human touch." Toyota believes that automation should be used to support human workers, not to replace them.
Toyota's production system is designed to stop automatically when a problem occurs. This gives workers time to fix the problem before it becomes a major issue.
7. Just-in-time
Just-in-time is a production system that involves producing only the parts that are needed, when they are needed. This helps to reduce waste and to improve efficiency.
Toyota uses a system of kanbans, or cards, to track the flow of parts through its production system. This system ensures that parts are delivered to the assembly line just in time to be used.
8. Heijunka: Leveling the workload
Heijunka is a Japanese word that means "leveling the workload." Toyota believes that it is important to level the workload throughout the production process to avoid bottlenecks.
Toyota uses a system of production smoothing to level the workload. This system involves producing a variety of products at different times throughout the day. This helps to keep the production line running smoothly and to reduce waste.
9. Poka-yoke: Mistake-proofing
Poka-yoke is a Japanese word that means "mistake-proofing." Toyota believes that it is important to design processes to prevent mistakes from happening in the first place.
Toyota uses a variety of poka-yoke devices to prevent mistakes. For example, the assembly line might be designed so that a part can only be installed one way, or a machine might be equipped with a sensor to detect a missing part.
10. Standardized work
Standardized work is a system of work that is designed to ensure that tasks are performed consistently and efficiently.
Toyota uses a system of standard operating procedures, or SOPs, to document the best way to perform each task. This helps to reduce variability and to improve quality.
11. Visual management
Visual management is a system that uses visual aids to make information easy to understand and accessible.
Toyota uses a variety of visual management tools, such as看板(kanban) boards, to track the flow of work and to identify problems.
12. Nemawashi: Consensus building
Nemawashi is a Japanese word that means "consensus building." Toyota believes that it is important to build consensus before making decisions.
Toyota uses a system of ringi to build consensus. This system involves circulating a proposed decision to all stakeholders for their feedback. This helps to ensure that everyone has a say in the decision-making process.
13. Ho-ren-so: Reporting, consultation, and follow-up
Ho-ren-so is a Japanese word that means "reporting, consultation, and follow-up." Toyota believes that it is important to keep everyone informed about what is going on and to follow up on decisions.
Toyota uses a system of daily reports to keep everyone informed about the progress of their work. The company also uses a system of regular meetings to discuss problems and to make decisions.
14. Kaizen Blitz
Kaizen Blitz is a rapid improvement event that is used to make significant improvements to a particular process or area in a short period of time.
Toyota uses Kaizen Blitz events to improve a variety of areas, such as product quality, productivity, and customer service. These events typically involve a team of employees who work together to identify and implement improvements.
The 14 Toyota management principles are a powerful set of tools that can be used to improve any business. These principles are based on the idea of continuous improvement and respect for people.
If you are looking to improve your business, I encourage you to learn more about the Toyota management principles and to start applying them to your own organization.
I believe that by following these principles, you can create a more successful and sustainable business.
4.8 out of 5
Language | : | English |
File size | : | 15513 KB |
Text-to-Speech | : | Enabled |
Screen Reader | : | Supported |
Enhanced typesetting | : | Enabled |
X-Ray | : | Enabled |
Word Wise | : | Enabled |
Print length | : | 449 pages |
Do you want to contribute by writing guest posts on this blog?
Please contact us and send us a resume of previous articles that you have written.
Book
Novel
Page
Chapter
Text
Story
Genre
Reader
Library
Paperback
E-book
Magazine
Newspaper
Paragraph
Sentence
Bookmark
Shelf
Glossary
Bibliography
Foreword
Preface
Synopsis
Annotation
Footnote
Manuscript
Scroll
Codex
Tome
Bestseller
Classics
Library card
Narrative
Biography
Autobiography
Memoir
Reference
Encyclopedia
Tess Sharpe
Krista Schlyer
Randy Christian
Julie Murphy
Kevin Kruse
Rita Carter
John Bemelmans Marciano
Patrick Forsyth
Jerzy Kosinski
Matthew J Milliner
Jeremy Bentham
Paul Stewart
Shannon O Bourne
Jenny Schwartz
Jennifer Lw Fink Rn Bsn
Jessica Walliser
Vijay Govindarajan
Rupert Wilkey
Stephen L Carter
Joseph Boyden
Light bulbAdvertise smarter! Our strategic ad space ensures maximum exposure. Reserve your spot today!
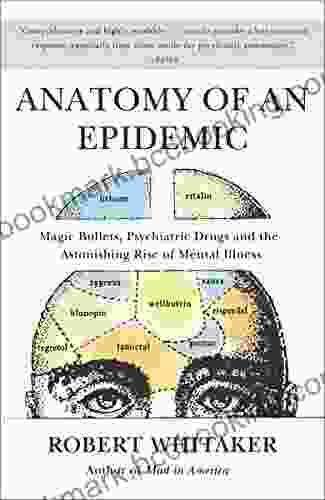

- Nick TurnerFollow ·19.9k
- Wesley ReedFollow ·18.4k
- Edmund HayesFollow ·3.1k
- Duane KellyFollow ·5.2k
- Jeremy CookFollow ·11.2k
- Ivan CoxFollow ·7.8k
- Hugh BellFollow ·14.5k
- Junichiro TanizakiFollow ·4.6k
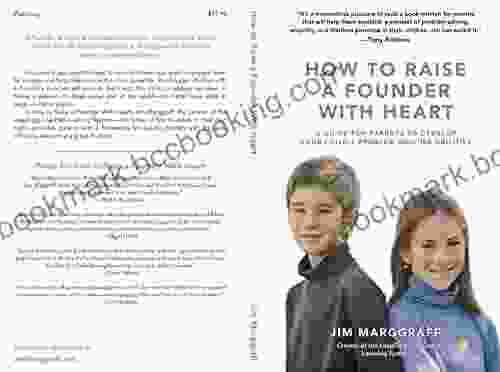

Guide for Parents: Unlocking Your Child's Problem-Solving...
As a parent, you...
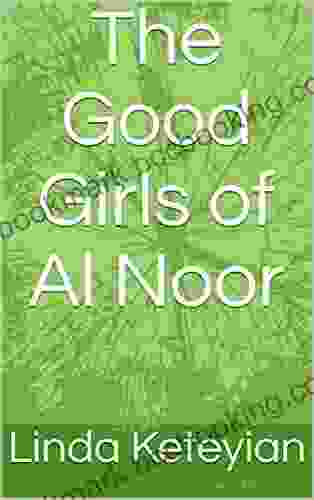

The Good Girls of Al Noor: A Gripping Tale of Hope and...
On March 15, 2019, a...
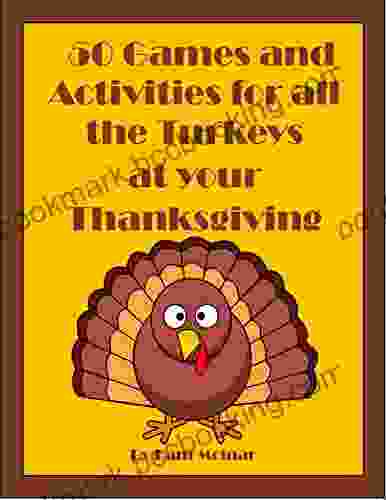

50 Games and Activities for All the Turkeys at Your...
Thanksgiving is a time for family, friends,...
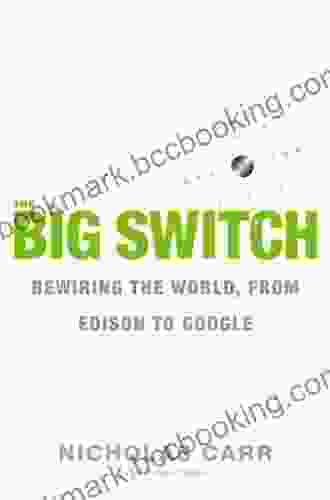

Rewiring the World: From Edison to Google - The...
A Captivating...
4.8 out of 5
Language | : | English |
File size | : | 15513 KB |
Text-to-Speech | : | Enabled |
Screen Reader | : | Supported |
Enhanced typesetting | : | Enabled |
X-Ray | : | Enabled |
Word Wise | : | Enabled |
Print length | : | 449 pages |